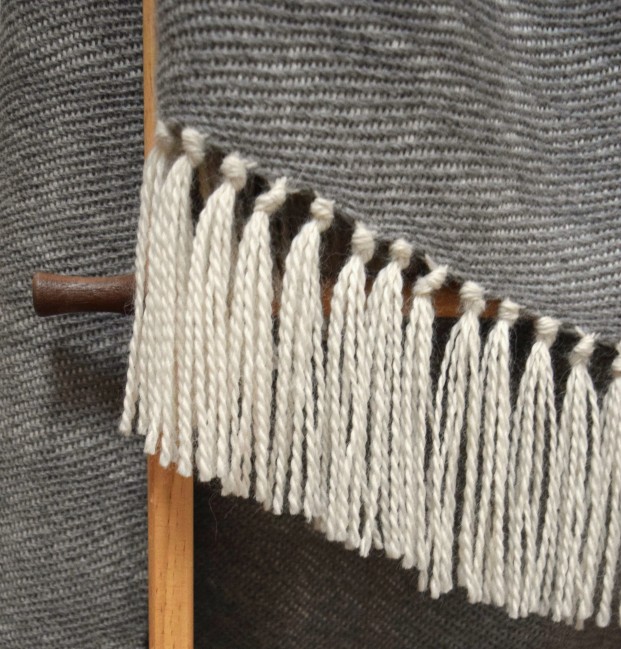
I have to confess mild disappointment, as I thought I could do better on my first twill project than I have. I planned it to be full width of 32″ and at least 72″ long. I planned it to be soft and fluffy and light, a lap blanket or shawl, whichever it wanted to be. But there was a double learning curve within this piece as not only have I not yet woven alpaca, which I realize now this particular superfine two ply worsted weight is quite slippery, but neither have I woven twill, or anything on multiple shaft loom. This was to be the first piece on the new table loom, a test run, using alpaca yarn that I happened to have the exact amount of in my yarn drawers, and meticulously planned to use up every yard of my light grey and cream that I had.
I set off with things going nearly right, having been lucky with the warping and keeping it organized, I had to improvise a front-to-back method. The work of sleying the reed and threading heddles entailed so much fussing I bore down under the yoke of determination and eventually, miraculously, got it done. Threading through the texsolv heddles in a straight draw, and finally with Jeff’s help I got it wound on to the warp beam nicely and firmly, with a lot of cardboard warp separators. Then there was testing the shed and fixing crossed threads for quite some time, not knowing what I was doing really, I really was at my limit. Presently, my first impression is that I don’t really love texsolv heddles, oh, yes, they’re quiet, and ultimately lightweight, just that threading them is a chore! I don’t know what wire heddles are like either, but they must be easier to thread.
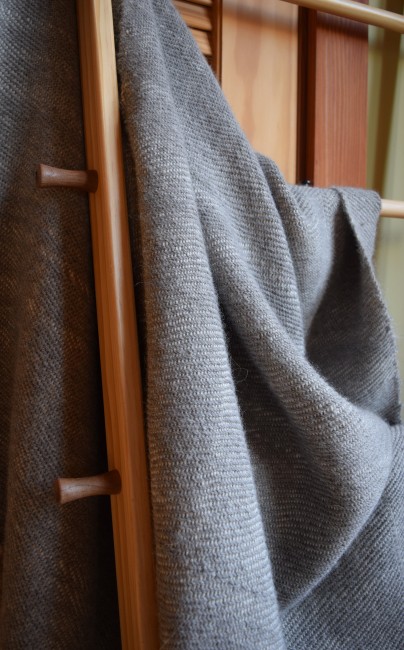
After I started my first few inches of weft, just about everything went wrong that could go wrong; warp threads started to break within the first 12 inches of weaving, as well as the floating selvedge, and I noticed how uneven the twill angle was, all over the place, beating so inconsistently as I am not use to a beater at all, it seemed I was barely pressing the weft into place. In retrospect I suspect that it is because the warp was too spread out, and I should have used at least one size smaller reed, if not two, and being so spread out, the weft just sunk heavily into place practically covering the warp, in some places almost like tapestry weaving. I did not and could not predict this weft-heavy twill because of my complete lack of experience. So now I know, especially for this alpaca that is slick, pack the warp in double that I have, and then I will have some choice about how the weft beats down.
I should be laughing, I knew so well that I’d make hash of the twill thing, but I also knew I’d learn a lot, and I most certainly did. The good news is that it was a lovely cold snowy morning yesterday when I brought this hand-made gift of goodwill over to my dearest friend (who agreed ahead of time to accept it as the learning curve it is), that I had finished it in time before it became hot as it does often in mid March, and who wants a heavy alpaca thing then? I am hopeful the alpaca will most certainly bloom and soften and become a perfect accessory in her rustic mountain cabin where it will now live, strewn over the back of some truly antique leather chair next to an old stone fireplace hearth, and even though it is lumpy, bumpy, and unintentionally striped with uneven twill angle, it will bloom out and fit in wonderfully.
Anyway, the list of Next Times are long and detailed and for documenting purposes, I have included them in my weaving notes below, and I shall find them useful in the future.

Special thanks to Ruth, the chat help at The Woolery, who has taught me more than any books or class!
♣ Weaving Notes ♣
- Yarn: Simply Alpaca by Knit Picks. Superfine alpaca, approx 12 wraps per inch, 247 yds = 100g. Color for warp is natural “Alaina”, and color for weft is light grey “Alfie”.
- Loom: Ashford 8-shaft Table Loom, 32″.
- Warping method: Traditional warping peg with cross, improvised back to front, but I forgot to measure the warp before winding on beam.
- Weft pattern: 2/2 twill.
- Selvedges: 1 end of floating selvedge each side.
- Number of warp ends: I ended up improvising adding some, doubling up some dents to try to use up all the warping yarn, and never counted.
- Reed: 8 dent.
- Sett after finishing: Warp 10 epi, and weft between 5 – 7 ppi.
- Finished: 30″ wide by 60″ long, plus a 5″ knotted fringe. I did not wash but steamed well.
- Yardage: Total yardage used = 1654 y, figured from weight (670g) of finished piece and not including loom waste.
- What I will do differently the next time I weave this alpaca:
- Start with way more than enough yarn, nearly double the amount I need for warp, so that being frugal doesn’t affect my planning!
- For this alpaca I will use a sett of 12 epi for plain weave, and perhaps 14 or 16 epi for twill. doubling ends through the 8 dent reed for twill. I do suspect the reason the twill is so weft heavy and at such a shallow angle is because of the warp being too spaced out, I don’t know actually, only a guess. Setting up the warp erring on too close probably better than too far apart, for the weaving would not stand up to even a light beat, as if it just wanted to squish together and the warp hardly visible.
- Originally I wanted to use my 10 dent reed that it came with, but didn’t think I could get the 72″ length full width of the loom, and I wanted it to be as wide as possible. So, I recalculated an epi of 9, and got an 8 dent reed, so I improvised 2 ends through one dent every 11 dents, it was crazy doing this, and I think it actually caused a vertical stripe in the warp ! As it ended up, I ran out of weft and had to cut the piece off the warp with another 12-18″ that could be woven –frugality backfired into waste! That was wasted warp that could have been reconfigured into a 10 or 12 dent reed for the warp I ended up using in the end. In future, it has got to be easier, a simple rule of start with plenty, and warp evenly 1 or 2 ends in the dent, every dent the same number of ends, all the way across the warp, with exception of the selvedges being more if reinforcing the edges.
- Not use the full width of the reed, this must be a universal thing, for one needs room for floating selvedges, and to add a couple of warps if necessary. Leave at least an inch on either side of the warp for fixes, at least until I know for sure, at least until I know what I’m doing.
- Add more twist to this alpaca if I can, before warping! The weft can be fluffy and barely twisted, that’s okay, but I would have had far fewer breaks had I run the balls through the spinning wheel giving them a couple of turns more.
- Warp it in even bundles of say, four inches on the reed, and sley/thread one bundle at a time rather than overwhelming myself with all of them at once. After all the threads are gone through the front, it is easy to untangle the warp with this slick alpaca, just a few shakes and the strands magically align, to wind on to the warping beam.
- As I was breaking warp threads, I was looking for things in the house I could wind and weight down as a floating weight. I discovered my tiny drop spindle to be the perfect warp weight!!! I loved it so much because I could actually spin and increase the twist of the yarn that was breaking because it was too loosely plied. So, bought another just like it, and plan to have two of these tiny less-than-an-ounce spindles to be my official floating selvedge weights, perhaps twisting two selvedge strands together rather tightly and “parking” it on the table, as those turkish style spindles do so well.


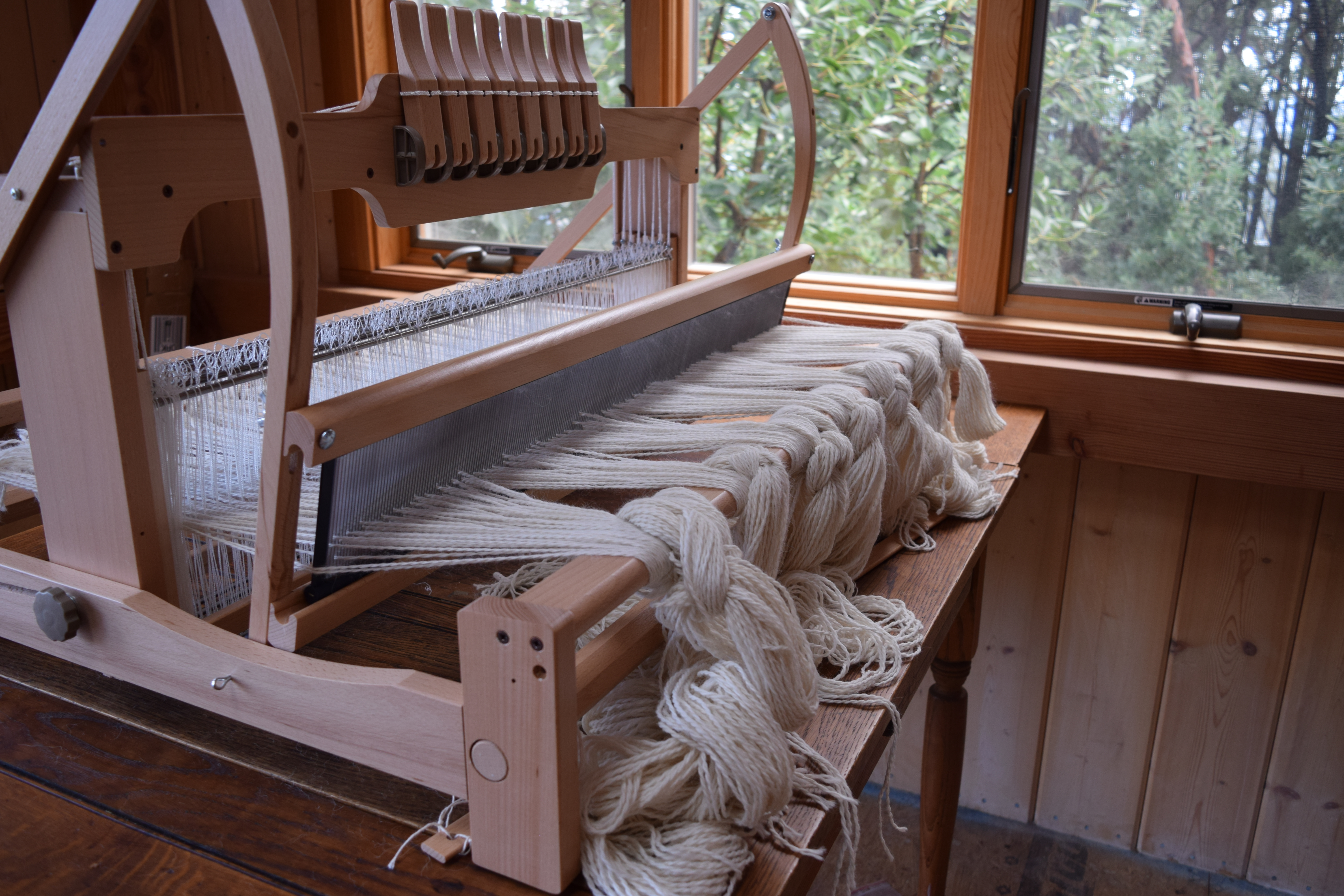
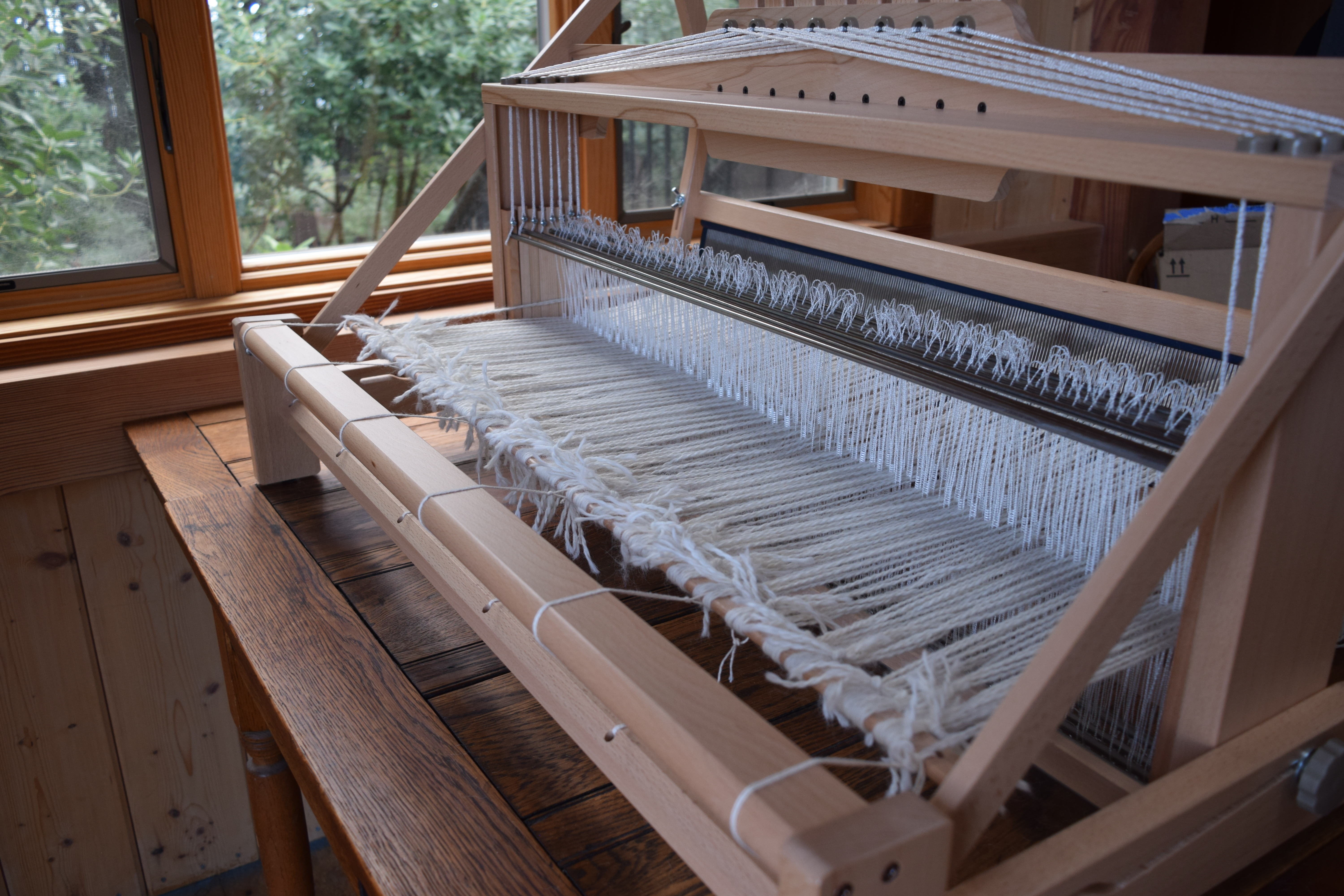
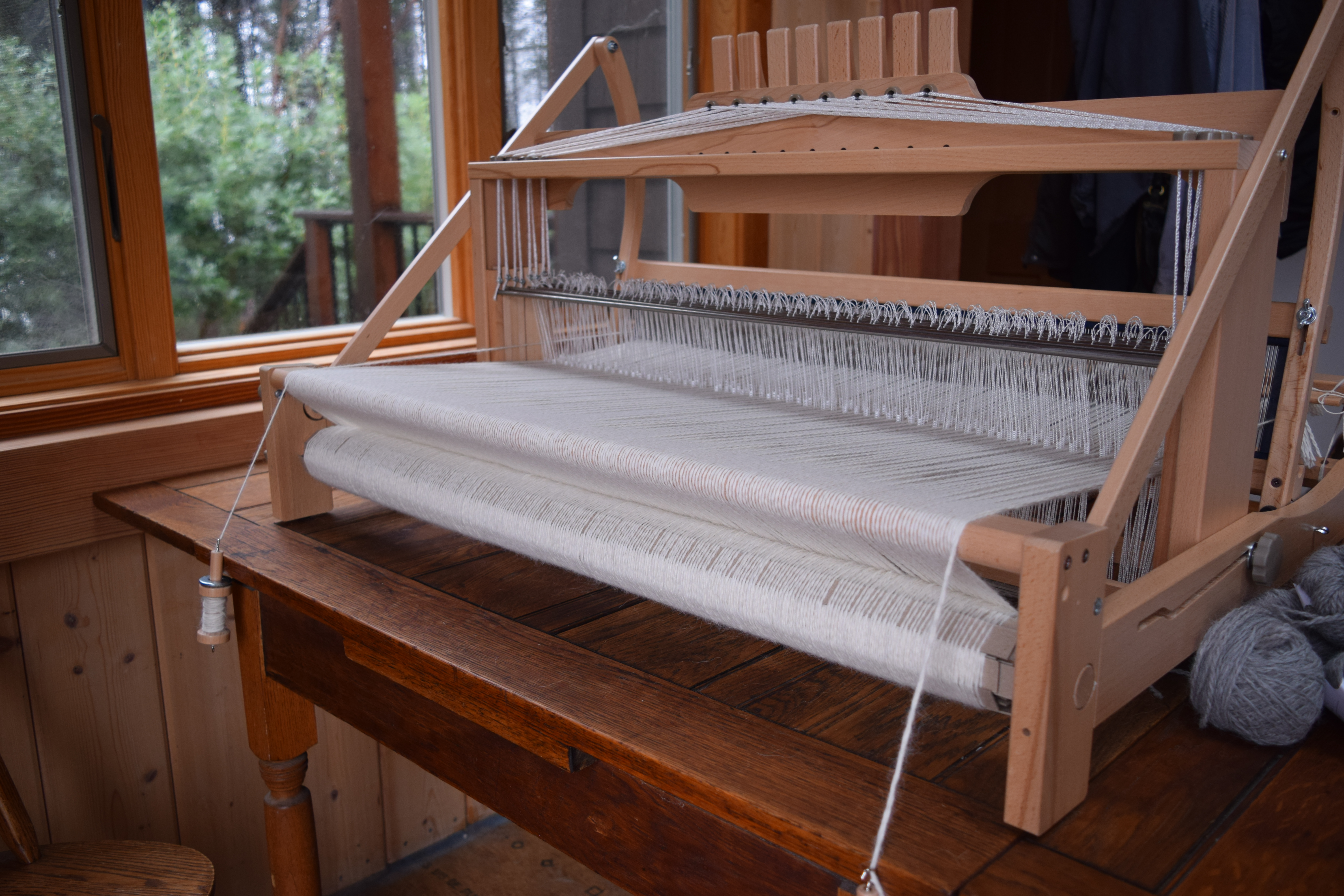
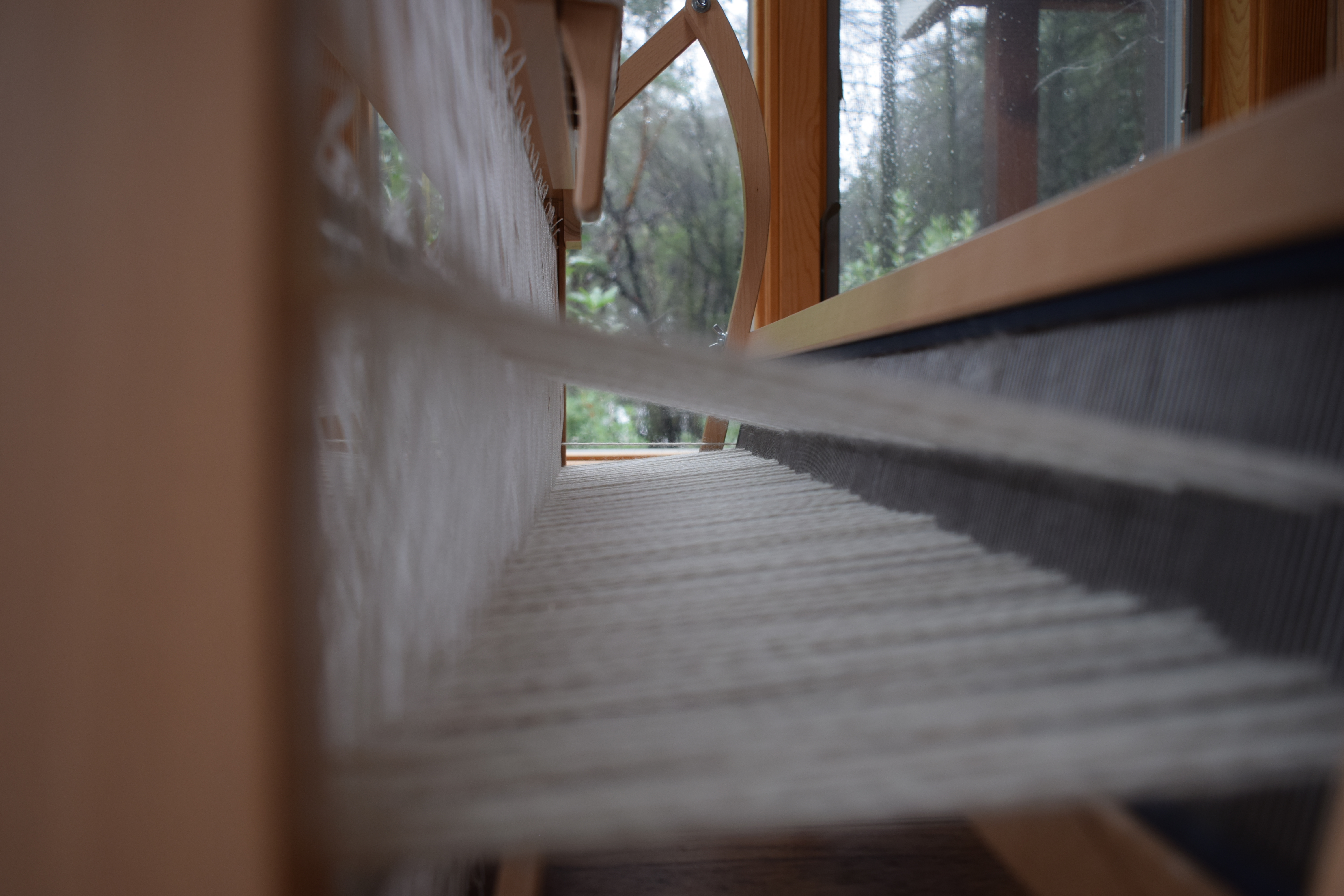
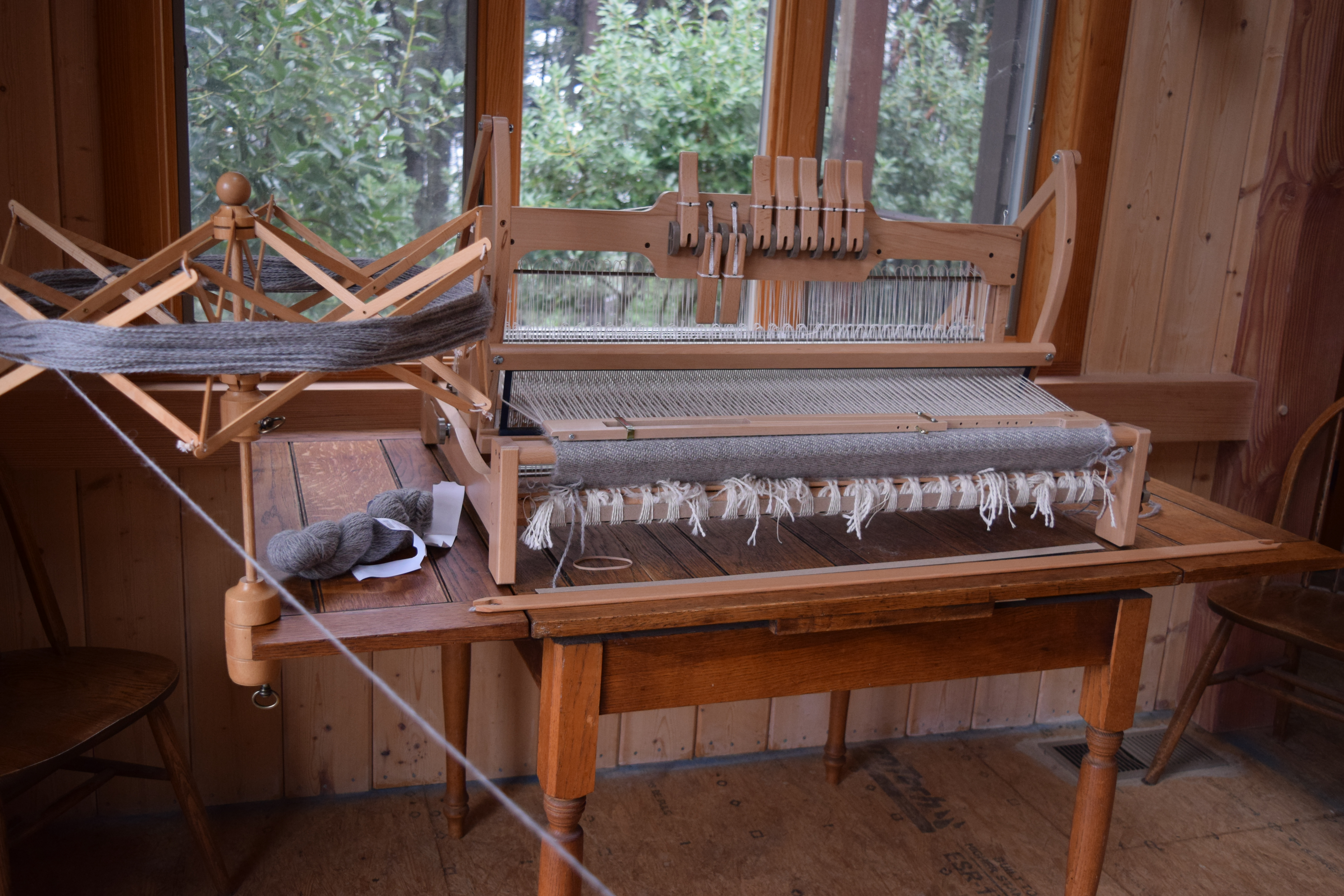

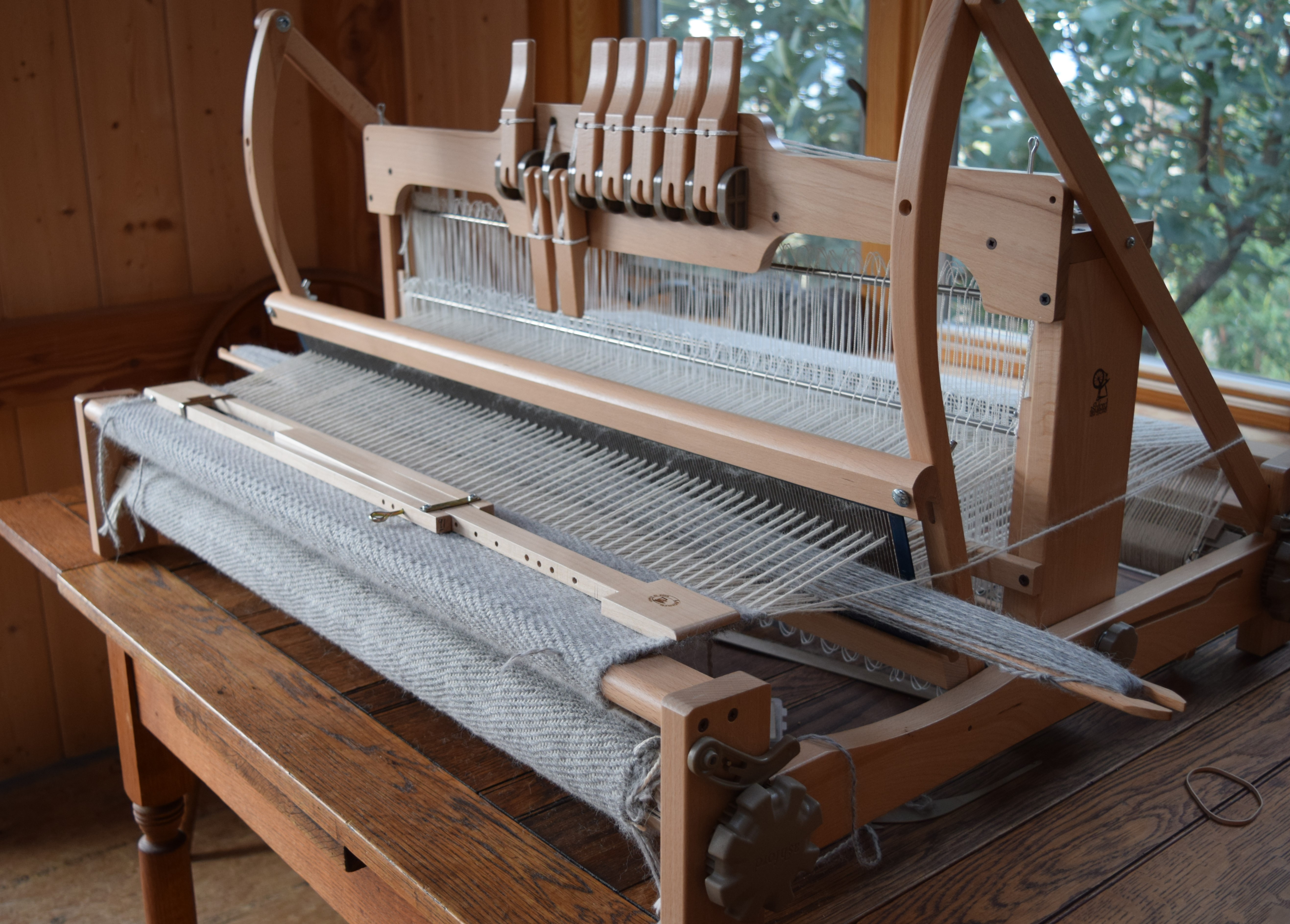
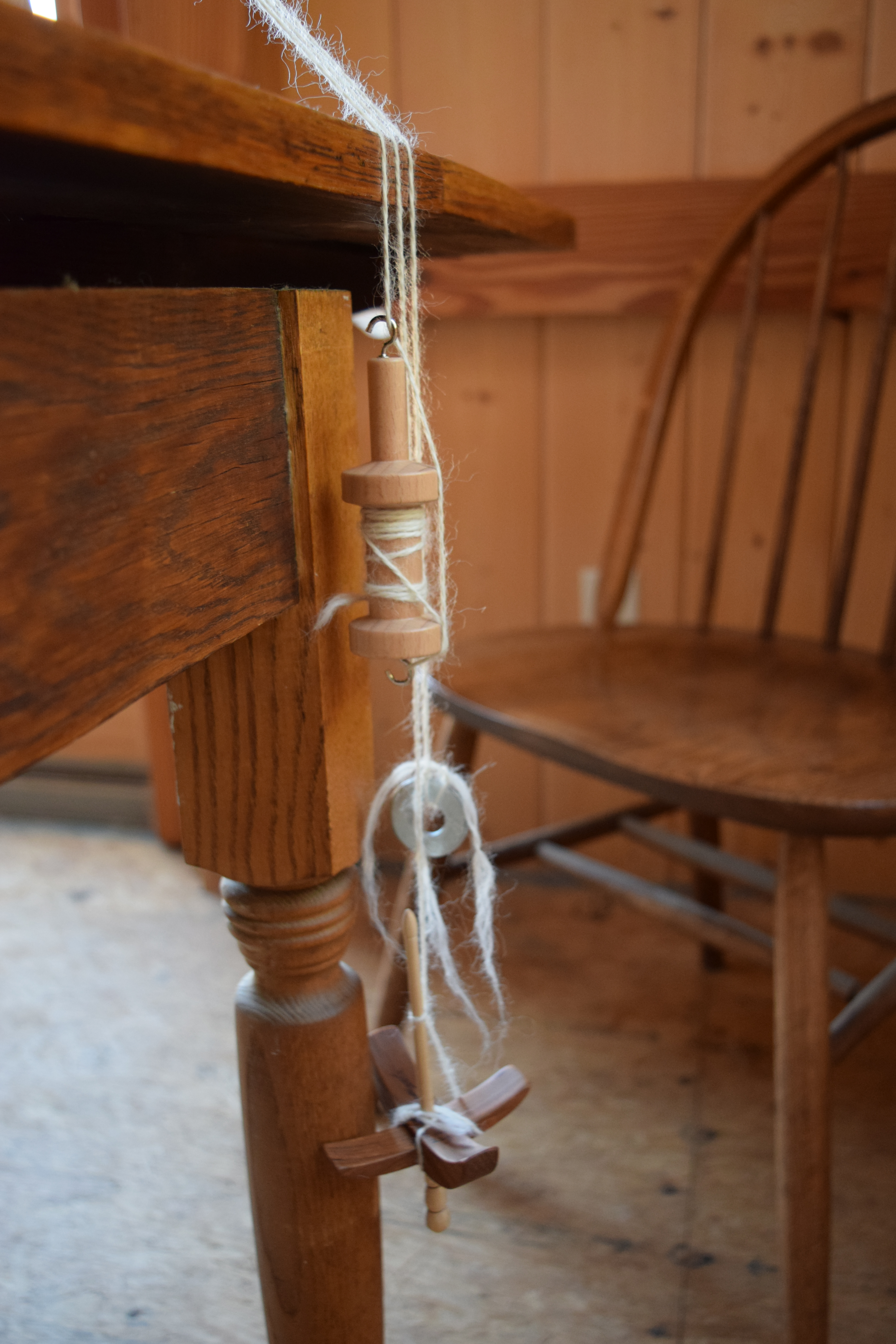
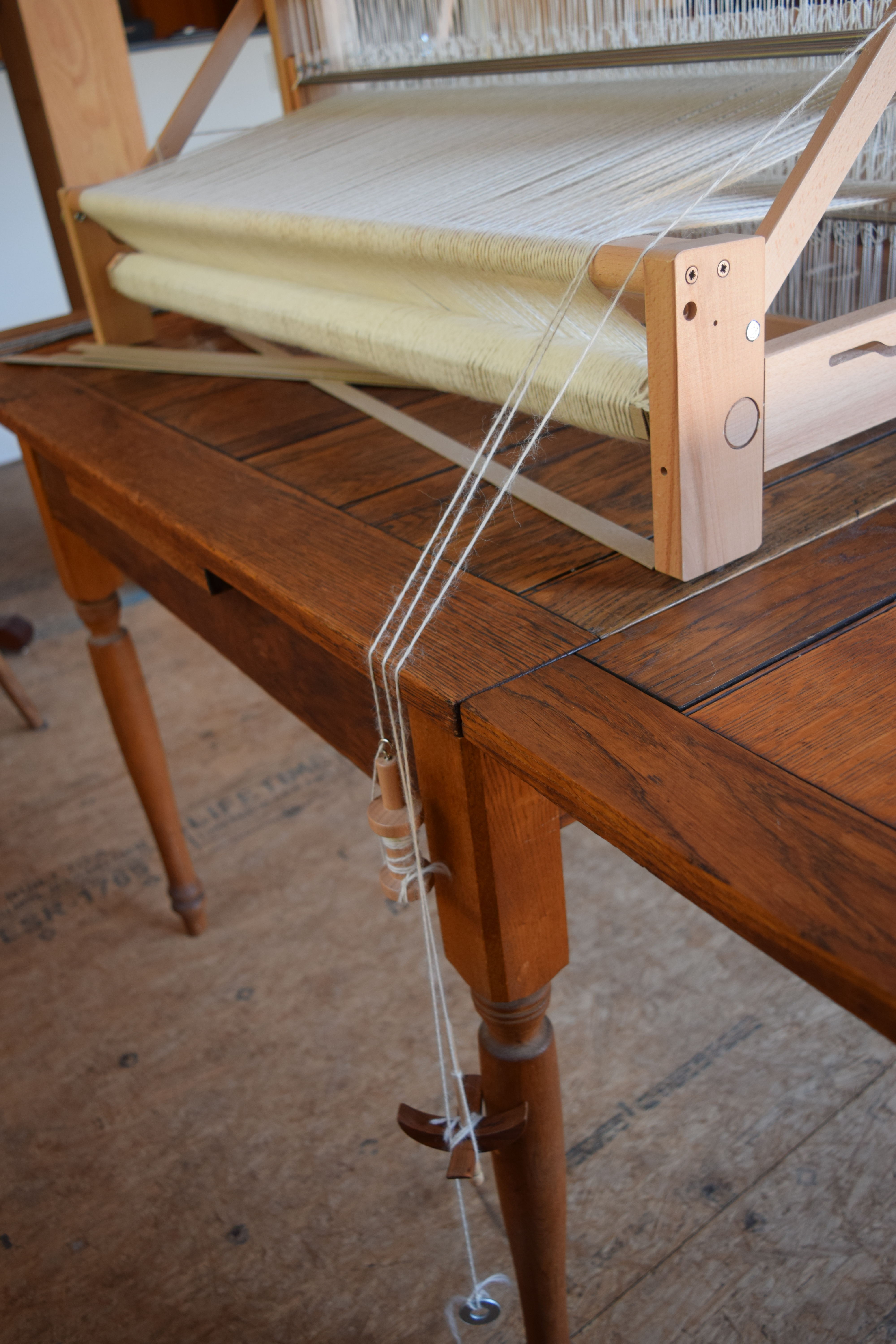

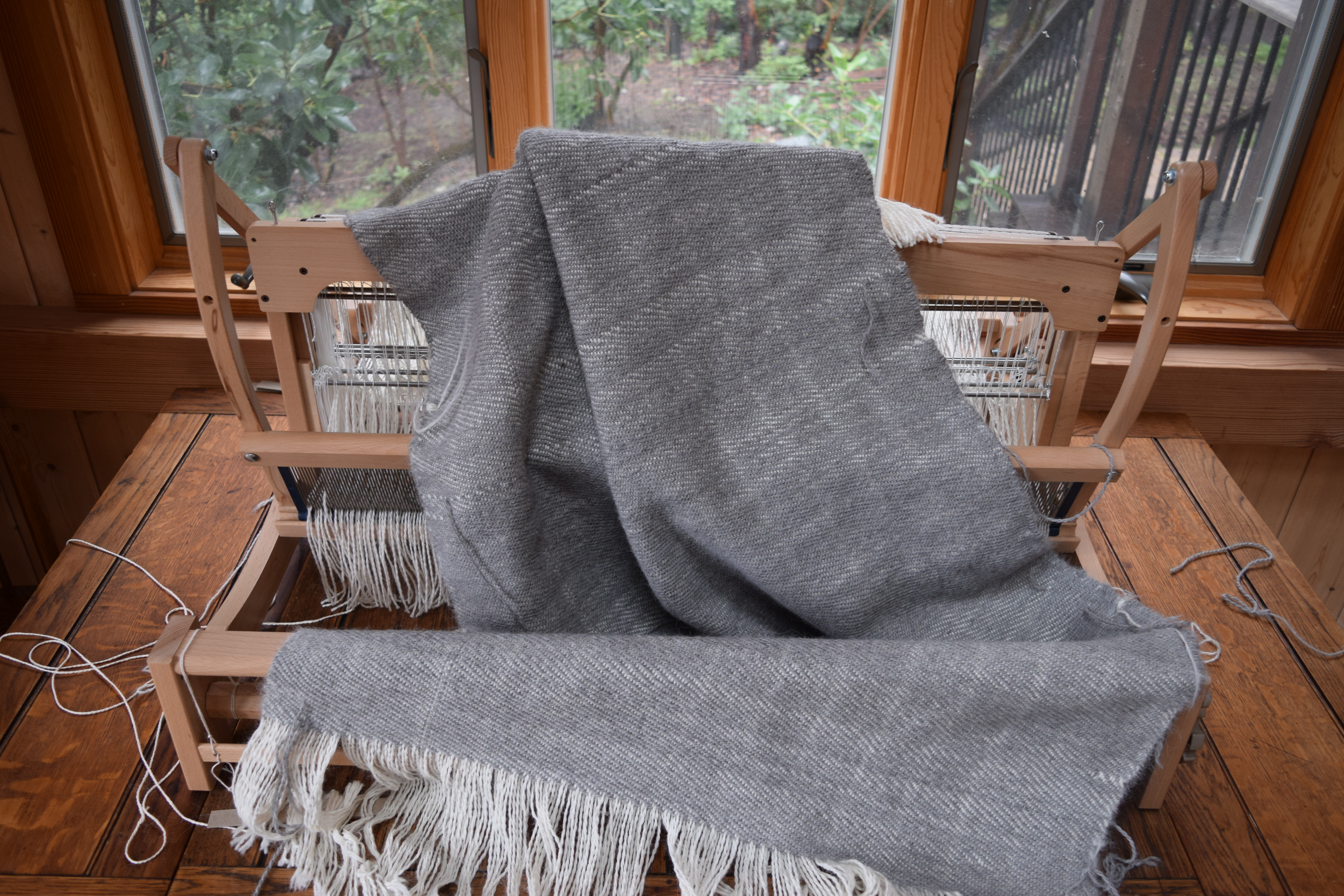
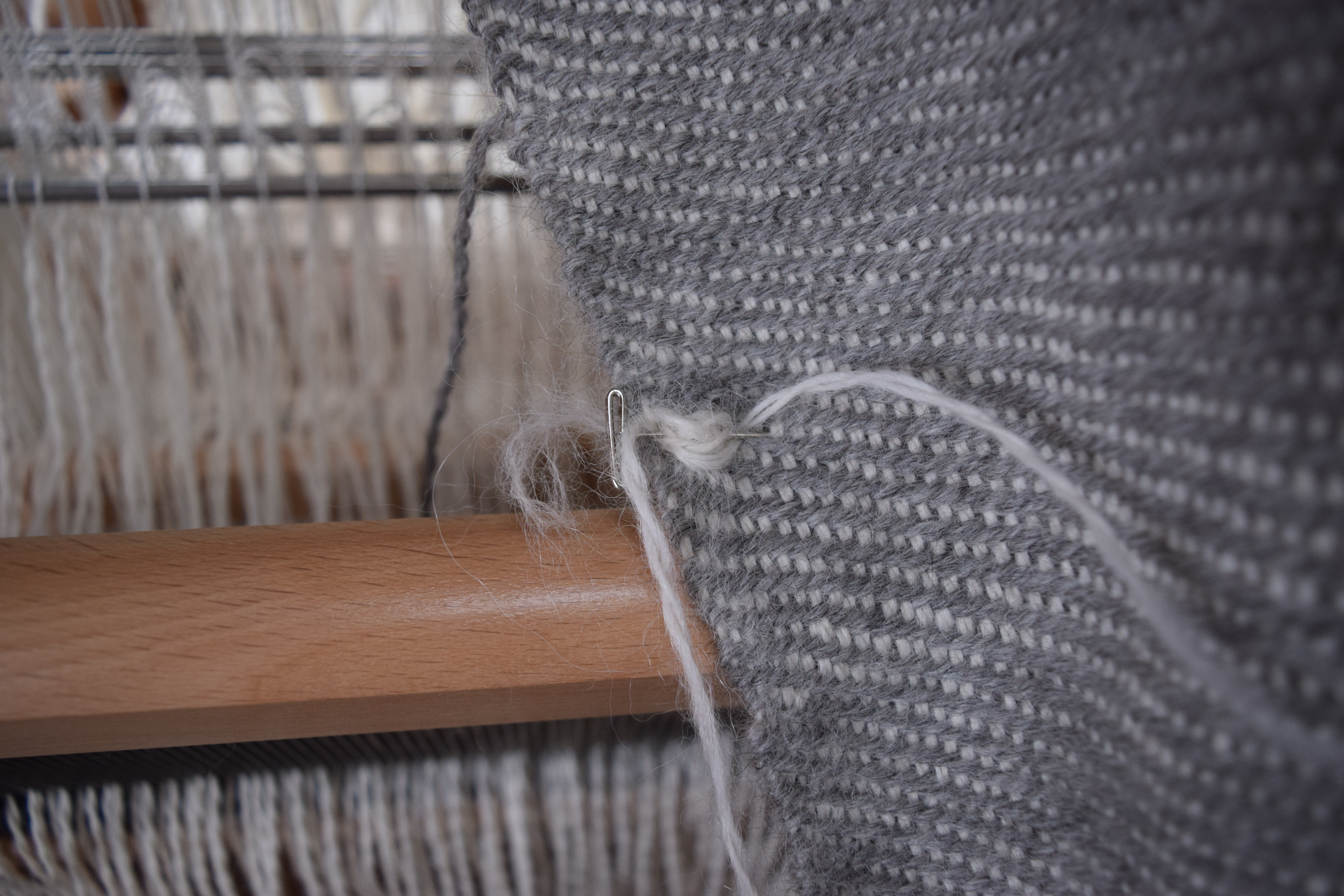
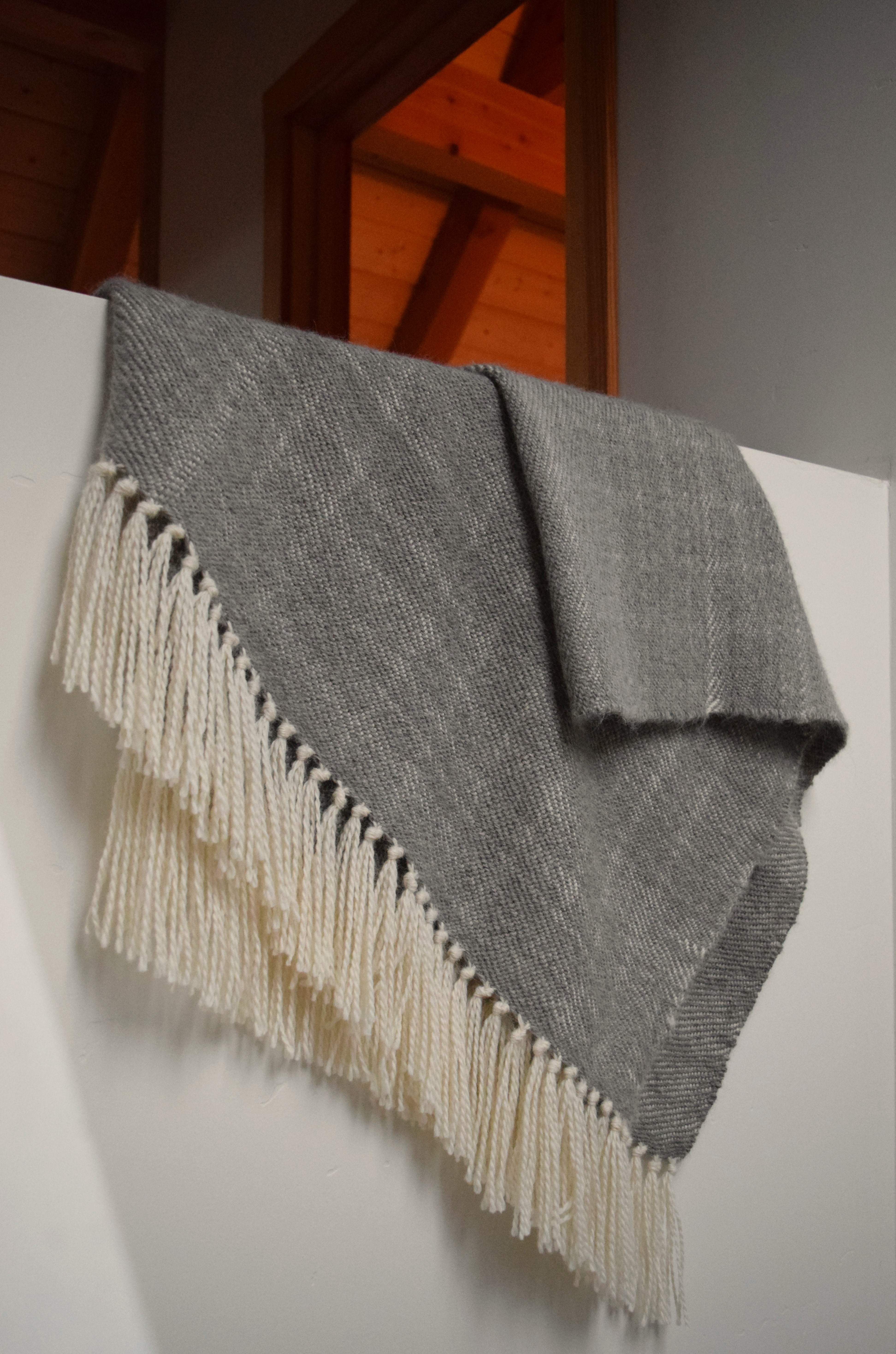
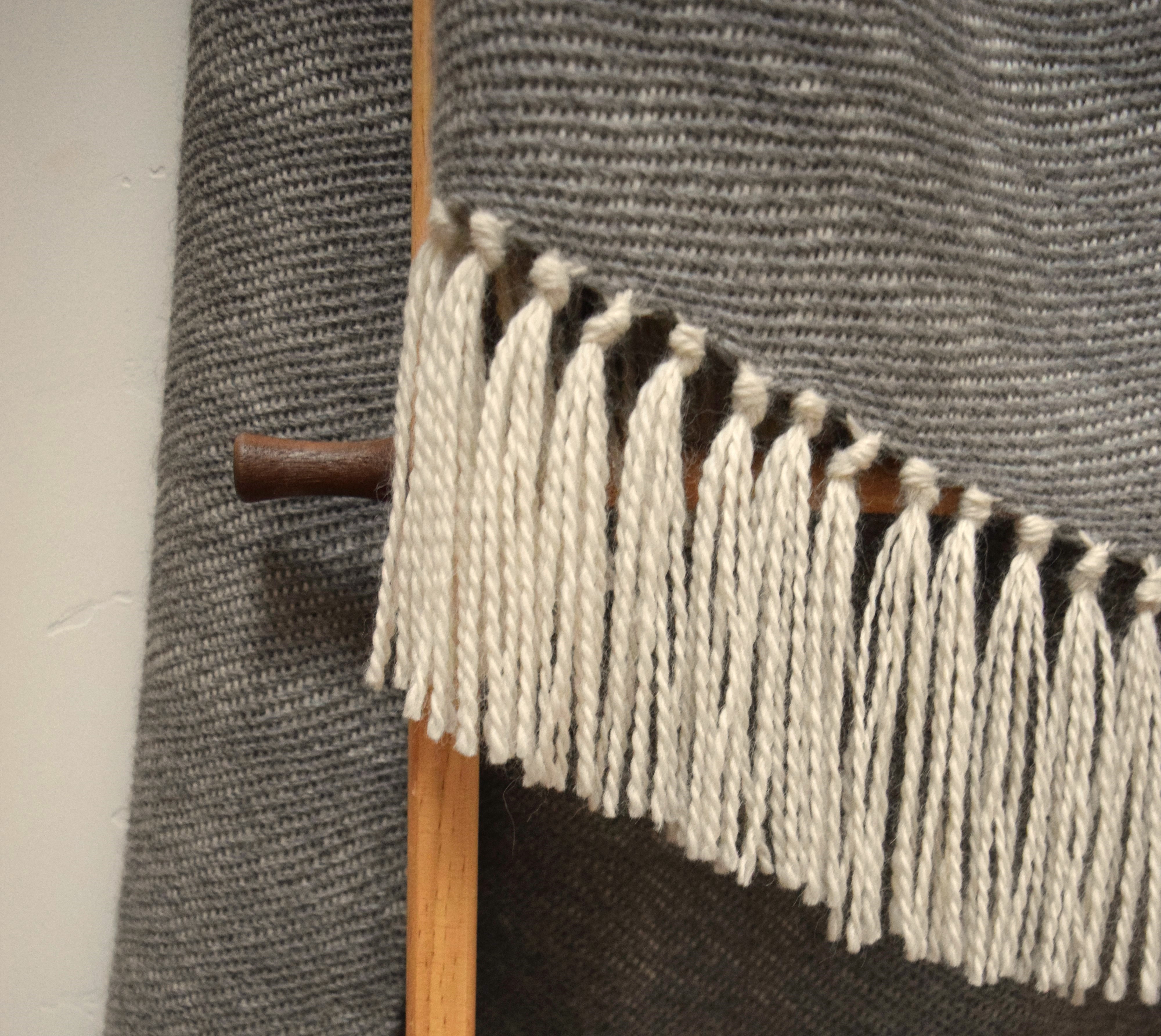
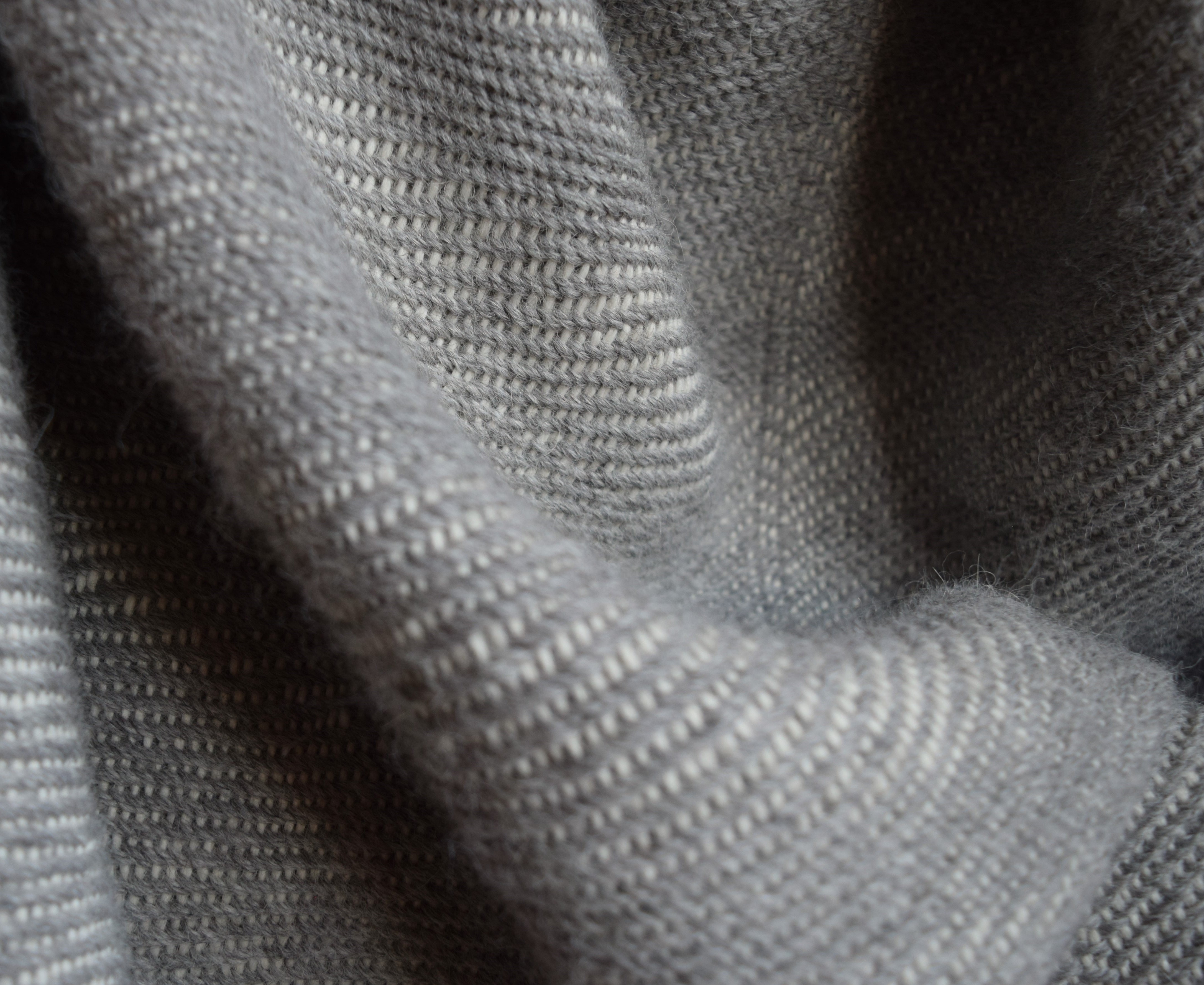

I love love love it! It is precious.
Thank you so much for loving it. I think it will look great on your old club chair or couch, or even your wingback . . . and when I come to visit you, sipping coffee next to the fire, will you cover me with it when it is cold? xx
Absolutely!
In spite of all the hurdles and frustrations, the final fabric is beautiful. I admire your “stick-to-it” attitude.
Thank you Regina, even though I am sharing my challenges and frustrations, really, I am enjoying learning weaving so much! xx